Workplace Safety Hazards: Identifying the Most Critical Threats to Employee Wellbeing
Understand workplace safety hazards
Workplace safety remain a critical concern across all industries, with certain hazards pose importantly greater risks to employee well bee than others. Identify the virtually dangerous threats help organizations prioritize safety measures and allocate resources efficaciously to protect their workforce.
The virtually likely factors to create unsafe working environments typically fall into several high risk categories that have systematically prove dangerous across various industries and workplace settings.
Chemical exposure and hazardous substances
Chemical hazards represent one of the near serious threats to workplace safety. These dangers oftentimes remain invisible until serious health consequences emerge, make them peculiarly insidious.
Improper storage of chemicals create immediate and long term risks. When hazardous substances lack proper containment, workers face exposure through inhalation, skin contact, or accidental ingestion. Manufacture facilities, laboratories, and clean operations often encounter these risks.
Inadequate ventilation systems compound chemical hazards importantly. Poor air circulation allow toxic fumes to accumulate, create dangerous concentrations that can cause respiratory problems, neurological damage, or chemical burns. Workers in paint shops, weld operations, and chemical processing plants face heighten exposure without proper ventilation controls.
Missing or inadequate personal protective equipment (pPPE)dramatically increase chemical exposure risks. When employers fail to provide appropriate respirators, chemical resistant gloves, or protective clothing, workers become vulnerable to substances that can cause immediate injury or long term health problems.
Faulty equipment and machinery
Defective or unwell maintain equipment create some of the virtually immediate and severe workplace dangers. These hazards can result in catastrophic injuries within seconds.
Machinery without proper safety guards expose workers to move parts that can cause crush injuries, amputations, or entanglement accidents. Manufacturing equipment, power tools, and industrial machinery require comprehensive safety systems to prevent contact with dangerous components.
Electrical equipment failures pose dual threats through electrocution risks and fire hazards. Damage wiring, overloaded circuits, or improperly ground equipment can deliver fatal electrical shocks or ignite workplace fires that spread chop chop.
Inadequate maintenance schedules allow equipment deterioration that lead to unexpected failures. When organizations defer maintenance to reduce costs, they create conditions where machinery can malfunction abruptly, potentially cause serious injuries to nearby workers.
Structural and environmental hazards
Physical workplace conditions importantly impact safety levels, with certain environmental factors create specially dangerous situations.
Poor lighting conditions increase accident risks across all workplace activities. Insufficient illumination make it difficult to identify hazards, read safety warnings, or operate equipment safely. Workers in murkily light areas face higher risks of trips, falls, and equipment relate injuries.

Source: masteringgrammar.com
Inadequate housekeeping create multiple hazard types simultaneously. Cluttered walkways, spill liquids, and accumulate debris increase slip and fall risks while potentially block emergency exits or create fire hazards.
Structural defects in buildings or work platforms pose serious collapse risks. Weakened floors, damage stairs, or compromise scaffolding can fail abruptly, cause fall from height or crush injuries.
Human factors and training deficiencies
Human behavior and knowledge gaps ofttimes amplify other workplace hazards, make proper training and safety culture essential for risk reduction.
Insufficient safety training leave workers unprepared to recognize and respond to hazards befittingly. Without proper education about risks and safety procedures, employees may inadvertently create dangerous situations or fail to protect themselves adequately.
Inadequate supervision allow unsafe practices to develop and persist. When supervisors lack safety knowledge or fail to enforce safety protocols systematically, workers may take shortcuts that increase injury risks.
Time pressure and production demands can override safety considerations. When organizations prioritize speed over safety, workers may skip protective measures or operate equipment beyond safe parameters to meet deadlines.
Communication and emergency preparedness failures
Effective communication systems and emergency procedures form critical safety infrastructure that prevent minor incidents from become major disasters.
Block or inadequate emergency exits can trap workers during fires, chemical releases, or other emergency situations. When exit routes remain obstructed or unwell mark, evacuation become difficult or impossible during critical moments.
Missing or non-functional emergency equipment, such as fire extinguishers, eyewash stations, or first aid supplies, prevent effective response to workplace accidents. Regular inspection and maintenance of emergency equipment ensure availability when need well-nigh.
Poor communication about hazards leave workers unaware of risks in their work areas. When hazard information fail to reach affected employees, they can not take appropriate protective measures.
Industry specific high risk factors
Certain industries face unique hazards that require specialized attention and safety measures.
Construction sites present multiple simultaneous hazards include fall from height, strike by accidents from fall objects, and equipment relate injuries. The dynamic nature of construction work create invariably change risk profiles.
Healthcare environments expose workers to biological hazards, include infectious diseases and contaminate materials. Needle stick injuries and exposure to corporal fluids create serious health risks for medical personnel.
Manufacture operations involve heavy machinery, chemical processes, and repetitive motions that can cause acute injuries or cumulative trauma disorders. The combination of multiple hazard types require comprehensive safety programs.
Identify the greatest risk factors
Among all potential workplace hazards, several factors systematically emerge as the virtually likely to create unsafe work environments:
Inadequate hazard communication stand out as a primary risk multiplier. When workers remain unaware of specific dangers in their workplace, all other hazards become more dangerous. This includes miss safety data sheets, inadequate warning signs, and poor training about chemical hazards.

Source: askfilo.com
Defective or miss safety equipment create immediate vulnerability to workplace hazards. This encompasses faulty machinery guardsnon-functionalal emergency equipment, and inadequate personal protective equipment.
Poor maintenance practices allow multiple hazard types to develop simultaneously. Deferred maintenance can lead to equipment failures, structural problems, and environmental hazards that compound risk levels.
Insufficient training and supervision create conditions where workers can not recognize or respond befittingly to workplace hazards. This human factor amplify all other risk categories.
Prevention and risk mitigation strategies
Effective workplace safety require systematic approaches that address the virtually critical risk factors comprehensively.
Regular hazard assessments help identify and prioritize safety risks before they cause injuries. These evaluations should examine physical conditions, equipment status, and work practices to uncover potential problems.
Comprehensive training programs ensure workers understand hazards and protective measures relevant to their specific job duties. Training should cover hazard recognition, proper equipment use, and emergency procedures.
Preventive maintenance schedules keep equipment and safety systems function decent. Regular inspections and maintenance prevent equipment failures that could create dangerous conditions.
Strong safety communication systems ensure hazard information reach all affected workers quickly. This includes safety meetings, hazard alerts, and clear signage throughout the workplace.
Create a culture of safety
Long term workplace safety depend on establish organizational cultures that prioritize worker protection over other considerations.
Management commitment to safety must be visible and consistent. When leaders demonstrate genuine concern for worker safety through actions and resource allocation, employees are more likely to follow safety procedures.
Worker participation in safety programs improve hazard identification and solution development. Employees who perform tasks every day frequently recognize risks that management might overlook.
Regular safety performance monitoring help identify trends and areas need improvement. Track incident rates, near misses, and safety compliance provide data for continuous improvement efforts.
Understand which factors are virtually likely to will create unsafe working environments will enable organizations to will focus their safety efforts where they’ll have the greatest impact. By address the highest risk factors consistently, employers can create safer workplaces that protect their virtually valuable asset – their employees.
MORE FROM jobsmatch4u.com
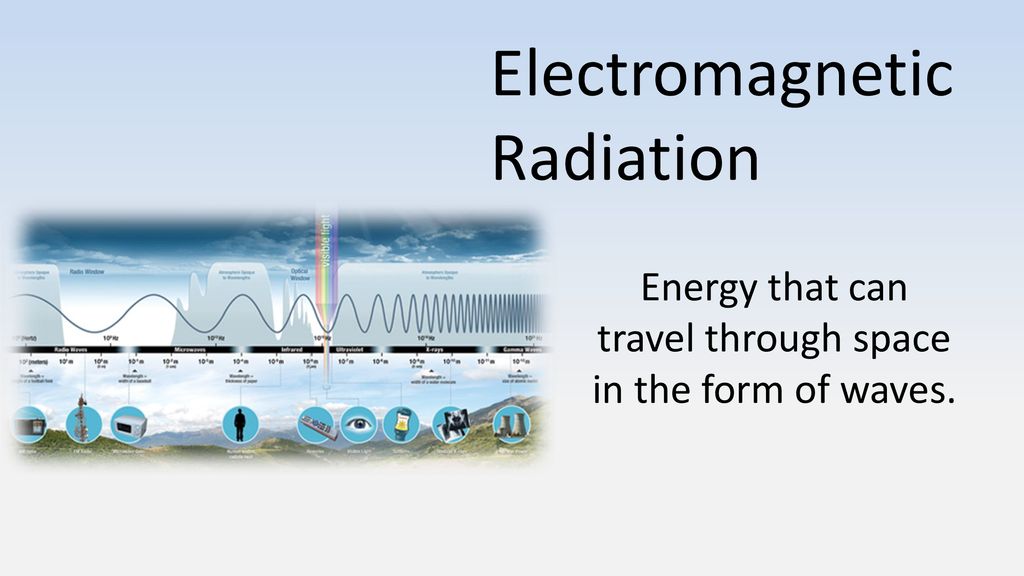
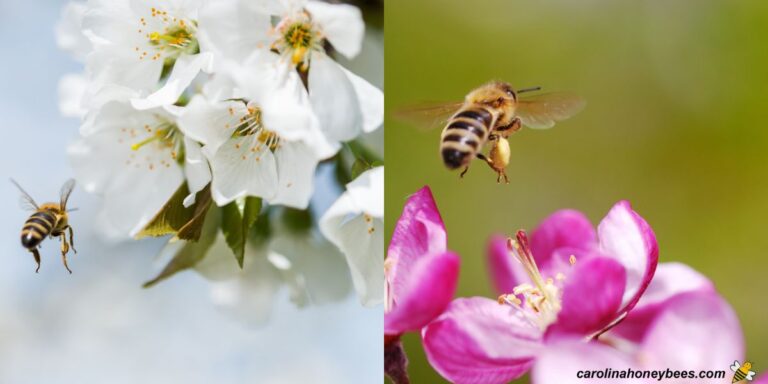
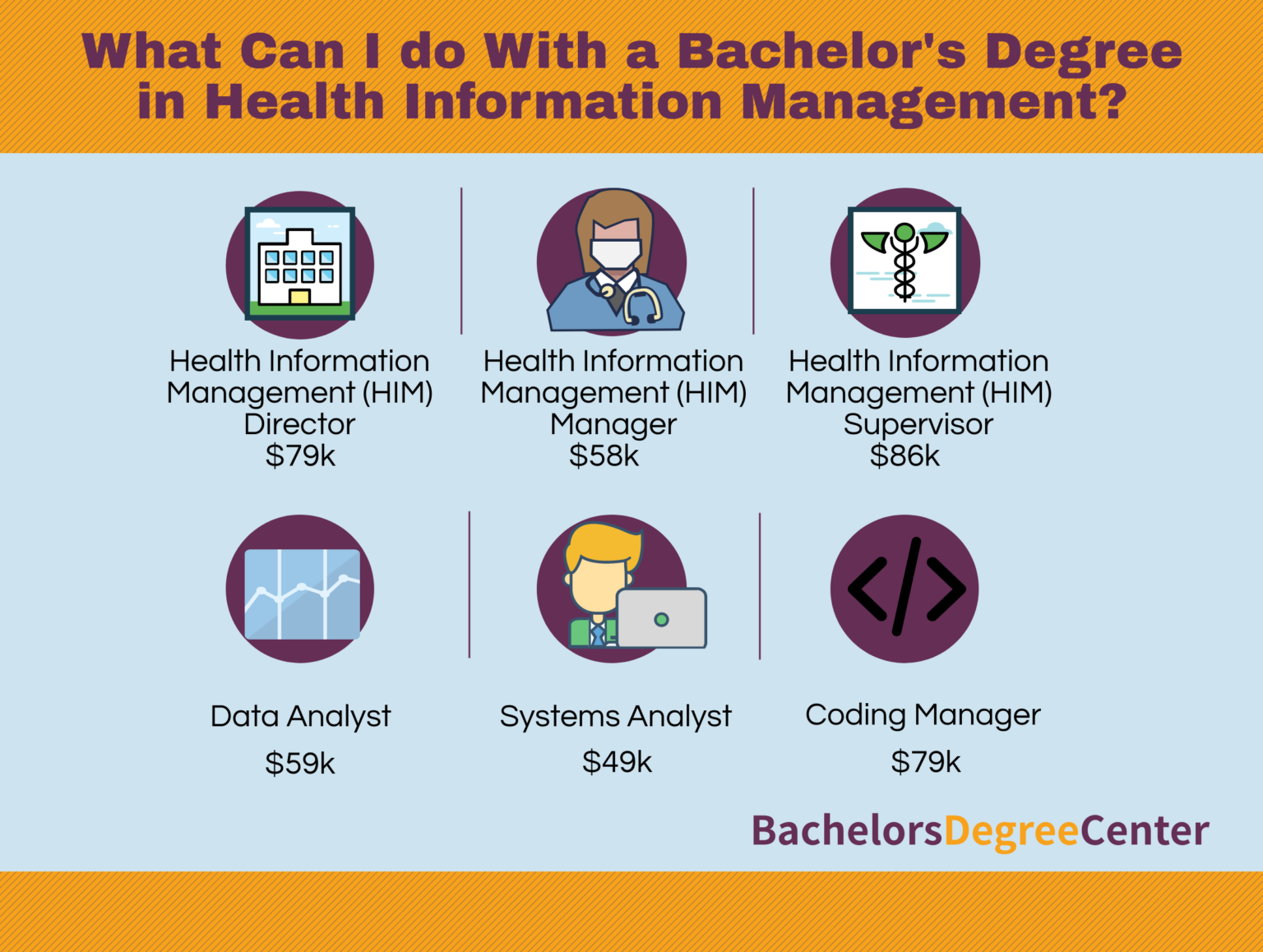
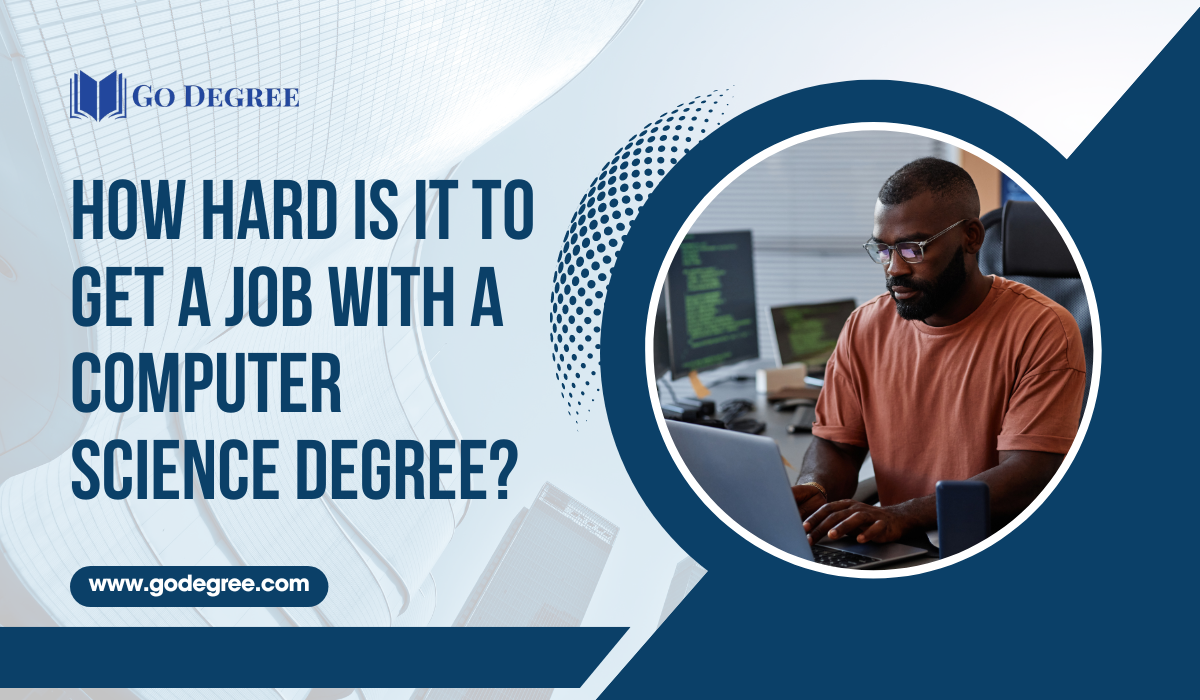
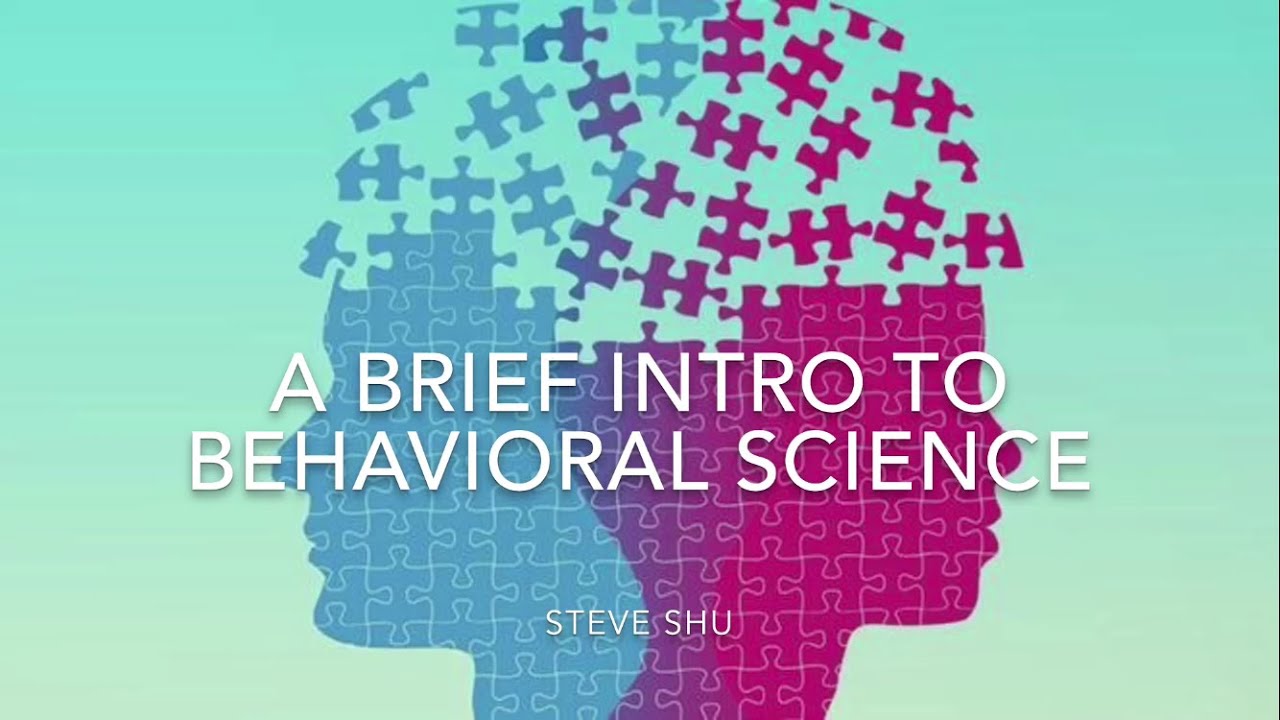
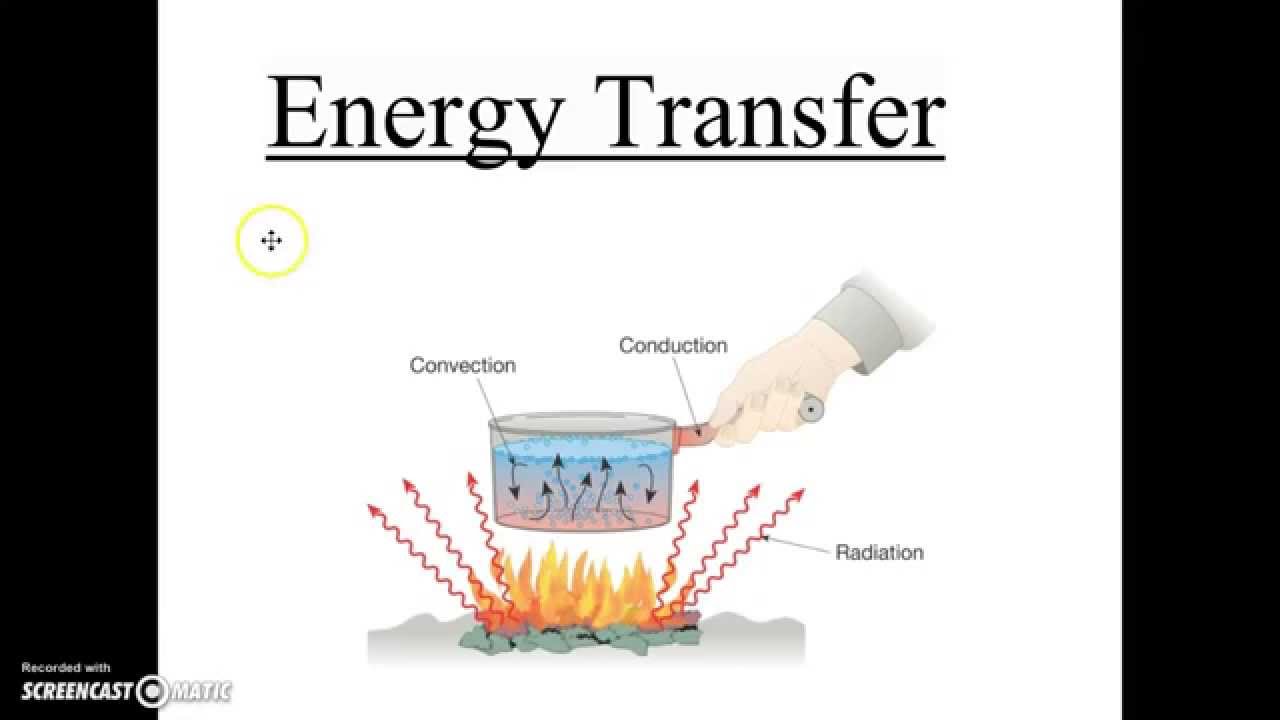
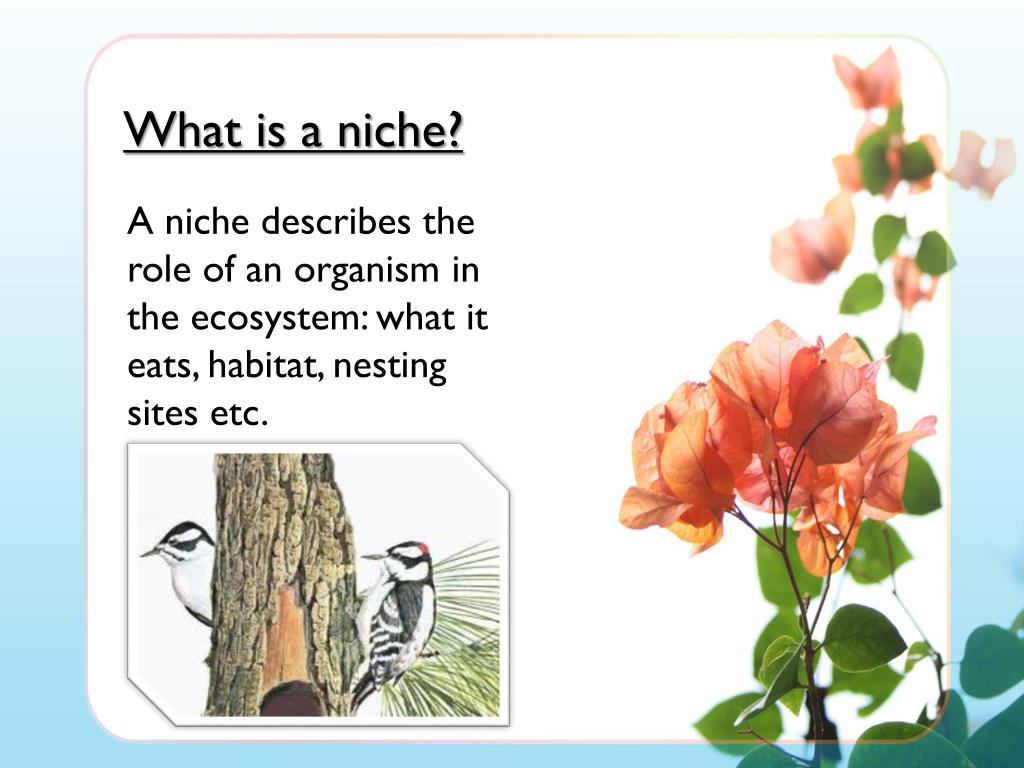
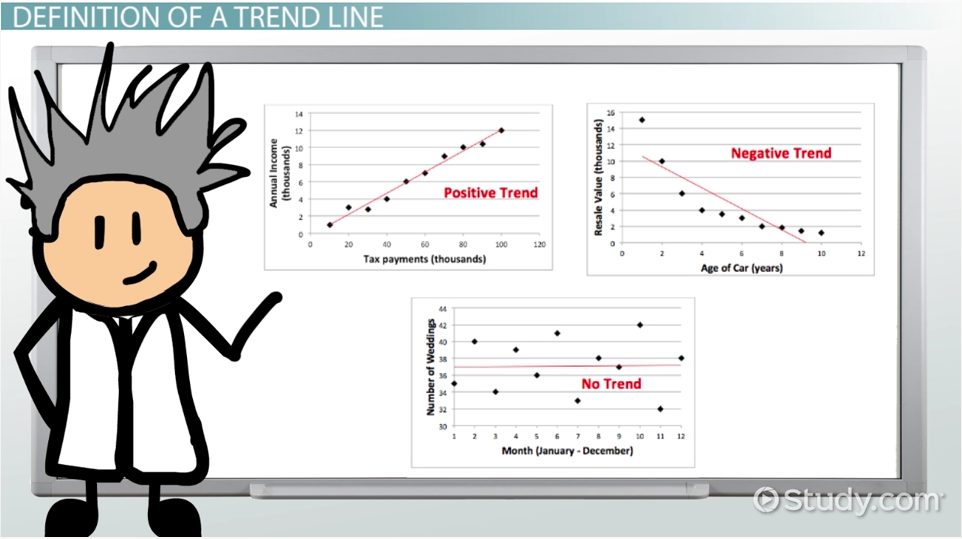
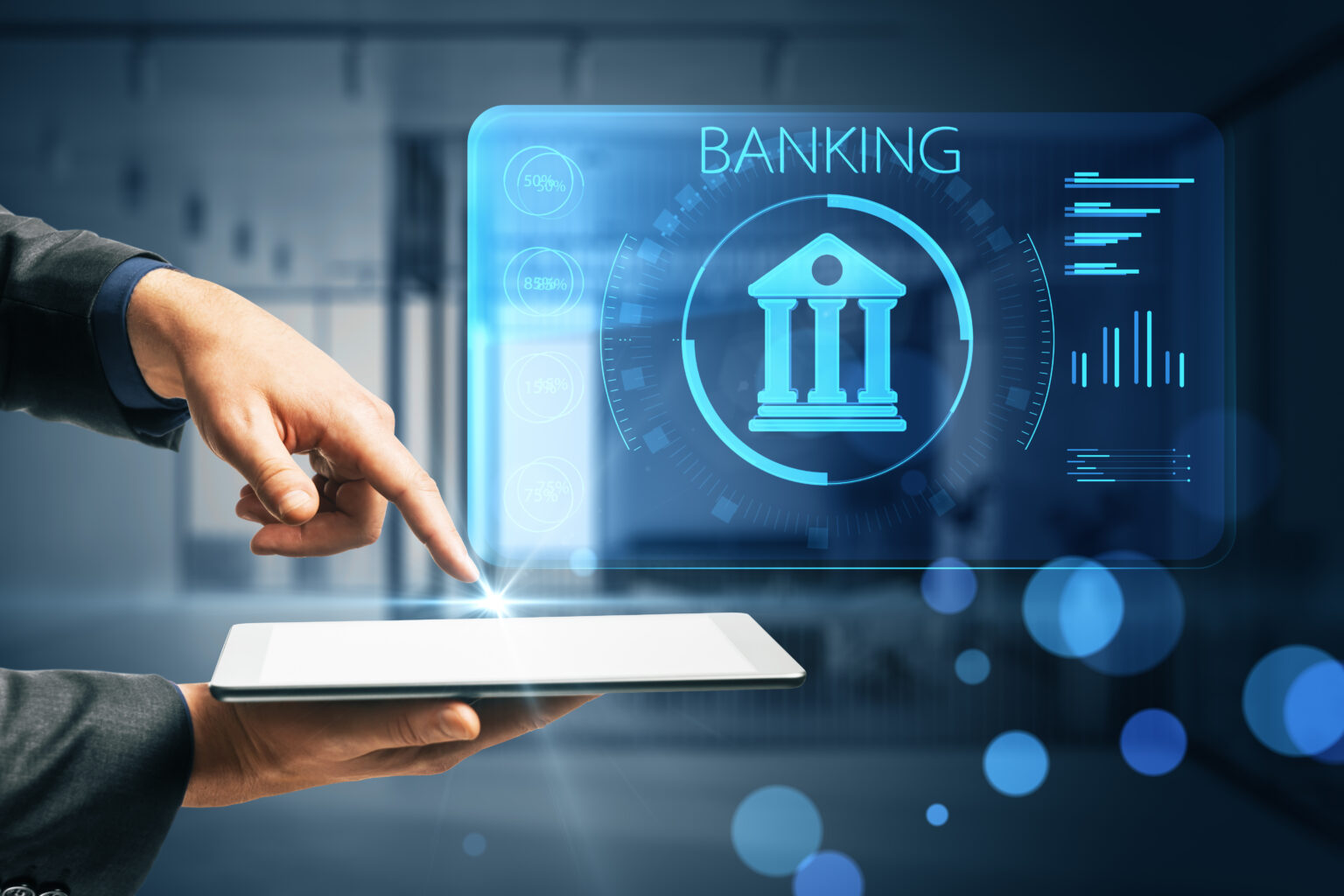
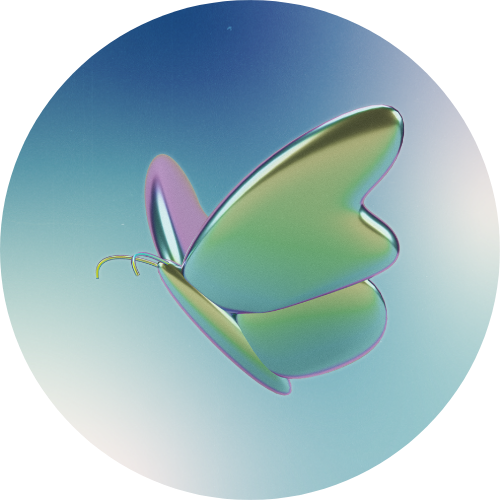
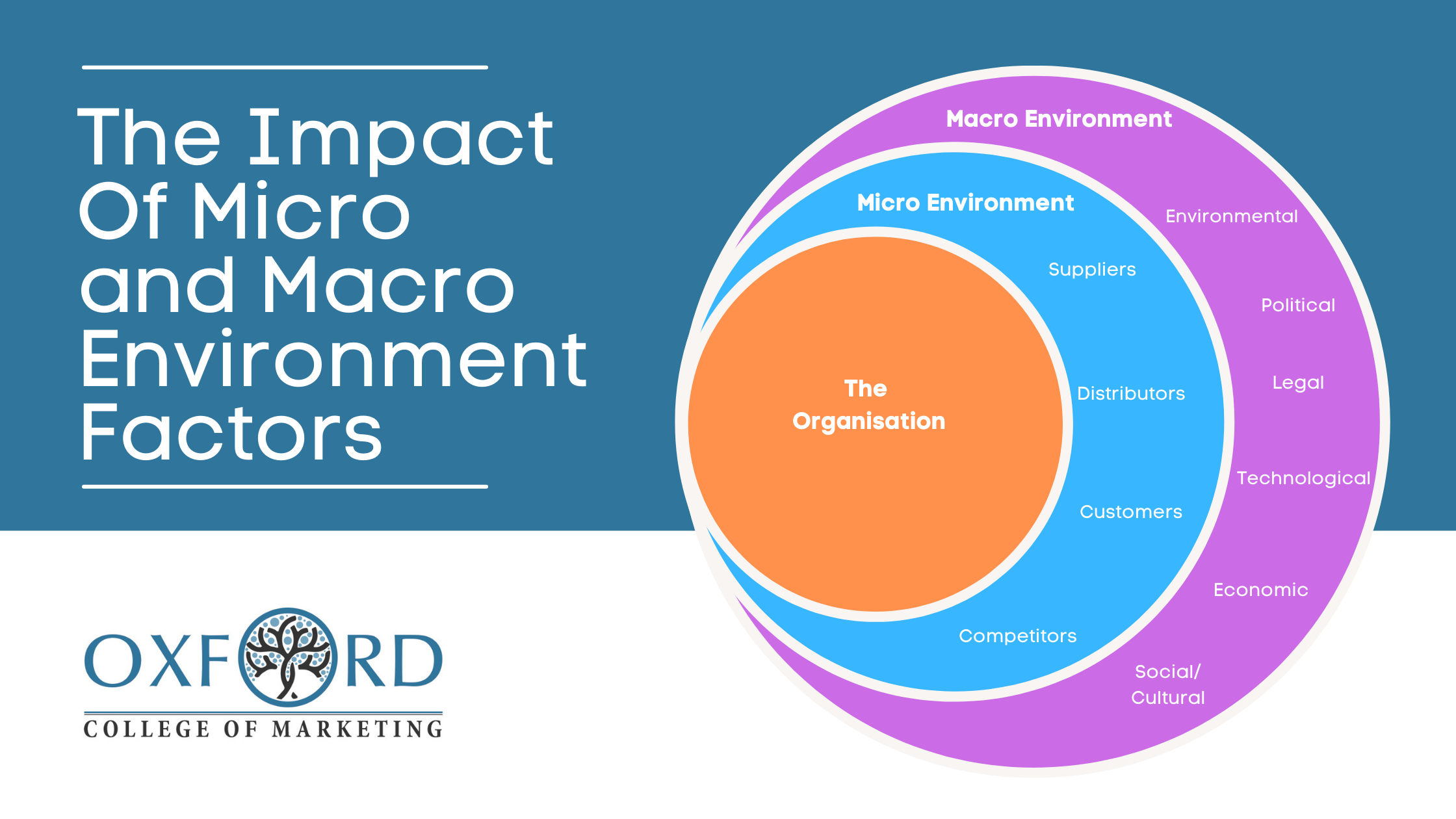
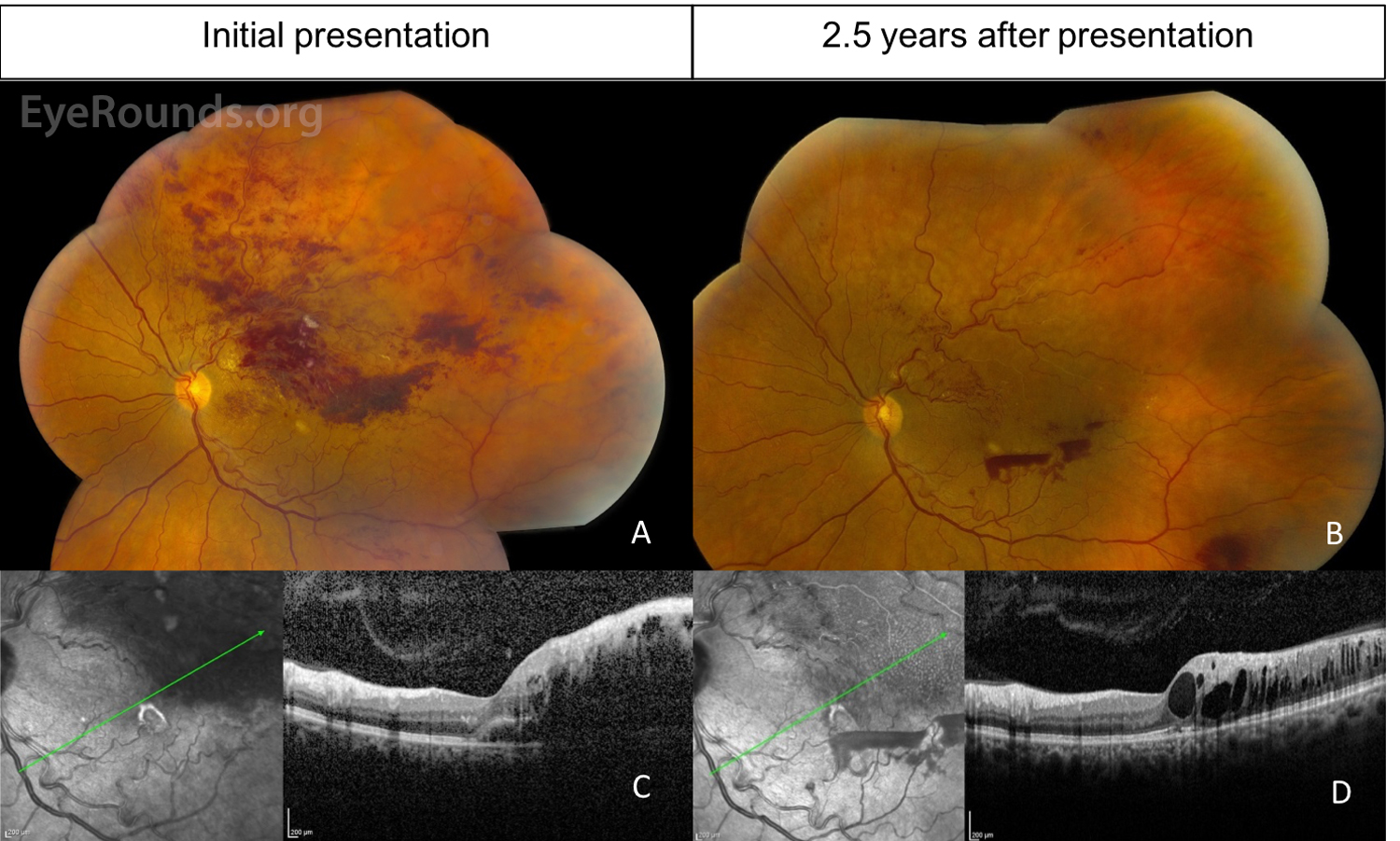