Industrial Painting: The Complete Guide to Commercial Coating Applications
What’s industrial painting?
Industrial painting refer to the application of protective and decorative coatings to commercial and industrial structures, equipment, and facilities. Unlike residential painting, industrial painting focus principally on functionality, durability, and protection kinda than aesthetics exclusively. These specialized coating systems are design to withstand harsh environments, chemical exposure, extreme temperatures, and physical wear.
The primary purpose of industrial painting is to extend the lifespan of assets, prevent corrosion, improve safety, and maintain operational efficiency in industrial settings. From manufacture plants and refineries to bridges and water towers, industrial painting play a crucial role in asset preservation across numerous sectors.
Types of industrial painting applications
Structural steel painting
Structural steel painting involve apply protective coatings to steel frameworks in buildings, bridges, and other load bear structures. These coatings prevent corrosion, which can compromise structural integrity. Typical coating systems include zinc rich primers, epoxy intermediates, and polyurethane topcoats that create a barrier against moisture, salt, and environmental contaminants.
Tank and vessel lining
Storage tanks and vessels oftentimes contain chemicals, oil, water, or other substances that can corrode metal surfaces. Specialized interior linings protect these containers from chemical attack while prevent product contamination. These linings must withstand specific chemical exposures, temperature fluctuations, and abrasion depend on the store materials.
Equipment and machinery painting
Industrial equipment require protective coatings to withstand operational stresses, include heat, vibration, and mechanical wear. These applications oftentimes involve specialized coatings that provide thermal resistance, chemical protection, or enhance visibility for safety purposes.

Source: profinishcoatings.com.au
Floor coatings
Industrial floor coatings create durable, chemical resistant surfaces in manufacturing facilities, warehouses, and process plants. Epoxy, polyurethane, and polyaspartic systems provide slip resistance, chemical protection, and easy cleaning while withstand heavy traffic and equipment loads.
Pipeline coatings
Pipelines transport oil, gas, water, or chemicals require specialized coatings to prevent corrosion and deterioration. These coatings must perform in bury, submerge, or expose conditions while resist soil stress, UV radiation, or marine environments.
Common industrial coating types
Epoxy coatings
Epoxy coatings offer exceptional adhesion, chemical resistance, and durability. They create hard, impermeable surfaces that withstand impacts and abrasion. Two component epoxies consist of a resin and hardener that, when mixed, create a chemical reaction result in a toughcross-linknk finish. These coatings excel in chemical plants, refineries, and food processing facilities.
Polyurethane coatings
Polyurethane coatings provide excellent UV stability, color retention, and gloss. They offer superior flexibility and abrasion resistance compare to epoxies. Oftentimes use as topcoats in coat systems, polyurethanes maintain appearance while provide weather resistance for exterior applications.
Zinc rich primers
Zinc rich primers provide cathodic protection to steel substrates. When scratch or damage, the zinc particles sacrifice themselves to protect the underlie steel through galvanic action. These primers form the foundation of many high performance coating systems for bridges, tanks, and marine structures.
In tumescent coatings
In tumescent coatings expand when expose to high temperatures, create an insulate char layer that protect structural steel from fire damage. These specialized coatings maintain structural integrity during fires, provide critical time for evacuation and emergency response in commercial and industrial buildings.
High temperature coatings
High temperature coatings withstand extreme heart conditions in furnaces, exhaust systems, and processing equipment. Silicone, ceramic, and inorganic zinc silicate formulations maintain protection at temperatures range from 400 ° f to over 1200 ° f, prevent scaling and oxidation.
The industrial painting process
Surface preparation
Surface preparation is the near critical phase of any industrial painting project. Proper preparation remove contaminants, create an appropriate surface profile, and ensure coating adhesion. Methods include:
-
Abrasive blasting:
Use sand, steel grit, or other media to remove rust, mill scale, and previous coatings while create an anchor profile for new coatings. -
Power tool cleaning:
Utilize grinders, needle guns, and wire brushes to remove loose contaminants and roughen surfaces. -
Solvent cleaning:
Remove oils, greases, and other contaminants use appropriate solvents. -
Chemical treatments:
Apply acid etches, phosphates, or conversion coatings to improve adhesion on certain substrates.
Industry standards like SSP ((ociety for protective coatings ))nd nacNACEn(ional association of corrosion engineers ) d)ine specific surface preparation requirements, from sspc SSP( solv(t cleaning ) to s)c sp1SSPnace no. NACEwell ni( well-nighst cleaning ).
)
Application methods
Industrial coatings are applied use various techniques depend on project requirements, coat properties, and environmental conditions:

Source: trexo.ca
-
Airless spray:
Hydraulic pressure forces coat through a small orifice, create a fan pattern without compressed air. This method provide high production rates and uniform film thickness for large areas. -
Conventional spray:
Combines coating material with compress air to atomize the paint. Offer excellent control for detailed work but create more overspray. -
Plural component spray:
Mix two part coatings (like epoxies )at the spray gun, eliminate pot life concerns for fasting cure materials. -
Brush and roller:
Manual application methods for smaller areas, touch ups, or when overspray must be avoided. -
Electrostatic spray:
Electrically charge coat particles to attract them to the ground substrate, improve transfer efficiency and reduce waste.
Quality control and inspection
Quality control ensure coating systems meet performance requirements through consistent inspection and testing:
-
Environmental monitoring:
Track temperature, humidity, and dew point to ensure application conditions meet manufacturer specifications. -
Wet film thickness (wft))
Measure coat thickness during application to predict dry film results. -
Dry film thickness (dDFT)
Verify final coating thickness use magnetic, electromagnetic, or ultrasonic gauges. -
Adhesion testing:
Confirm proper bonding between coat layers and substrate use pull off or cross-cut tests. -
Holiday testing:
Detect pinholes or voids in coatings use low voltage wet sponge or high voltage spark testing.
Industries serve by industrial painting
Oil and gas
The oil and gas industry require specialized coatings for refineries, offshore platforms, storage tanks, and pipelines. These coatings must withstand chemical exposure, temperature extremes, and harsh environments while meet strict safety standards.
Power generation
Power plants utilize industrial coatings on boilers, cool towers, turbines, and structural components. These applications protect against corrosion, heat degradation, and environmental exposure in critical infrastructure.
Water and wastewater
Water treatment facilities require specialized coatings for clarifiers, digesters, filters, and pipe systems. These coatings prevent corrosion while maintain water quality and safety in potable water and wastewater applications.
Manufacture
Manufacture facilities use industrial coatings to protect equipment, production lines, and build components from chemical exposure, wear, and contamination. These coatings enhance safety, improve cleanliness, and extend asset life.
Transportation infrastructure
Bridges, highways, airports, and marine structures require durable coating systems to withstand weather exposure, traffic wear, and environmental stresses. These applications protect critical infrastructure while reduce maintenance costs.
Benefits of professional industrial painting
Asset protection and extended lifespan
Right apply industrial coatings can extend asset life by 15 30 years by prevent corrosion, chemical attack, and environmental degradation. This protection translate into significant cost savings compare to premature equipment replacement or structural repairs.
Safety enhancement
Industrial coatings improve workplace safety through fire protection, slip resistance, chemical containment, and hazard identification. Color code systems for pipes, equipment, and safety zones enhance visual communication and reduce accidents.
Operational efficiency
Smooth, decent coat surfaces improve fluid flow in pipes, reduce cleaning time, minimize product contamination, and enhance heat transfer in process equipment. These improvements increase productivity and reduce operational costs.
Regulatory compliance
Industrial coatings help facilities meet environmental, safety, and industry specific regulations. Low VOC formulations, food grade certifications, and fire-resistant coatings ensure compliance while reduce liability.
Challenges in industrial painting
Environmental considerations
Industrial painting must address environmental regulations regard volatile organic compounds (vvows) hazardous air pollutants, and waste disposal. The industry continue to develop water base, high solids, and powder coat alternatives to traditional solvent base systems.
Safety concerns
Industrial painting involve potential hazards include chemical exposure, fall risks, confine space entry, and respiratory dangers. Comprehensive safety programs, proper training, and appropriate personal protective equipment are essential for worker protection.
Application constraints
Weather conditions, production schedules, and facility operations can restrict painting activities. Projects oftentimes require careful planning to minimize downtime, coordinate with other trades, and work within narrow application windows.
Select an industrial painting contractor
Choose the right industrial painting contractor involve evaluate several key factors:
-
Experience and specialization:
Contractors with specific experience in your industry understand unique requirements and challenges. -
Certifications and training:
Look for SSP qup((uality procedure ))ertifications, manufacturer approvals, and document training programs. -
Safety record:
Review EMR (experience modification rate )ratings, osOSHAompliance history, and comprehensive safety programs. -
Equipment and capabilities:
Ensure the contractor have appropriate equipment for surface preparation, application, and quality control. -
Project management:
Evaluate planning processes, documentation systems, and communication protocols for complex projects. -
Warranty and support:
Consider the scope and duration of workmanship warranties and ongoing maintenance support.
Future trends in industrial painting
Smart coatings
Emerge smart coating technologies incorporate sensors, indicators, or responsive elements that detect corrosion, temperature changes, or structural stresses. These advanced coatings provide real time monitoring of asset conditions without additional instrumentation.
Sustainable formulations
The industry continue to develop eco-friendly coating options with reduce environmental impact. Water base systems, powder coatings, and high solids formulations minimize VOC emissions while maintain performance requirements.
Automated application
Robotics and automated systems progressively handle industrial painting tasks in hazardous or difficult to access areas. These technologies improve consistency, reduce worker exposure, and enhance productivity for repetitive applications.
Conclusion
Industrial painting represent a specialized discipline that combine materials science, application expertise, and quality control to protect valuable assets across numerous industries. Air beyond simple decoration, these engineer coating systems provide critical protection against corrosion, chemical attack, fire damage, and environmental degradation.
When decent specify and apply, industrial coatings deliver significant return on investment through extended asset life, reduce maintenance costs, improve operational efficiency, and enhance safety. As technology advances, industrial painting continue to evolve with more sustainable formulations, improve application methods, and innovative coating properties.
Understand the fundamentals of industrial painting help facility owners, project managers, and maintenance professionals make informed decisions about protect their valuable industrial assets for the long term.
This text was generated using a large language model, and select text has been reviewed and moderated for purposes such as readability.
MORE FROM jobsmatch4u.com
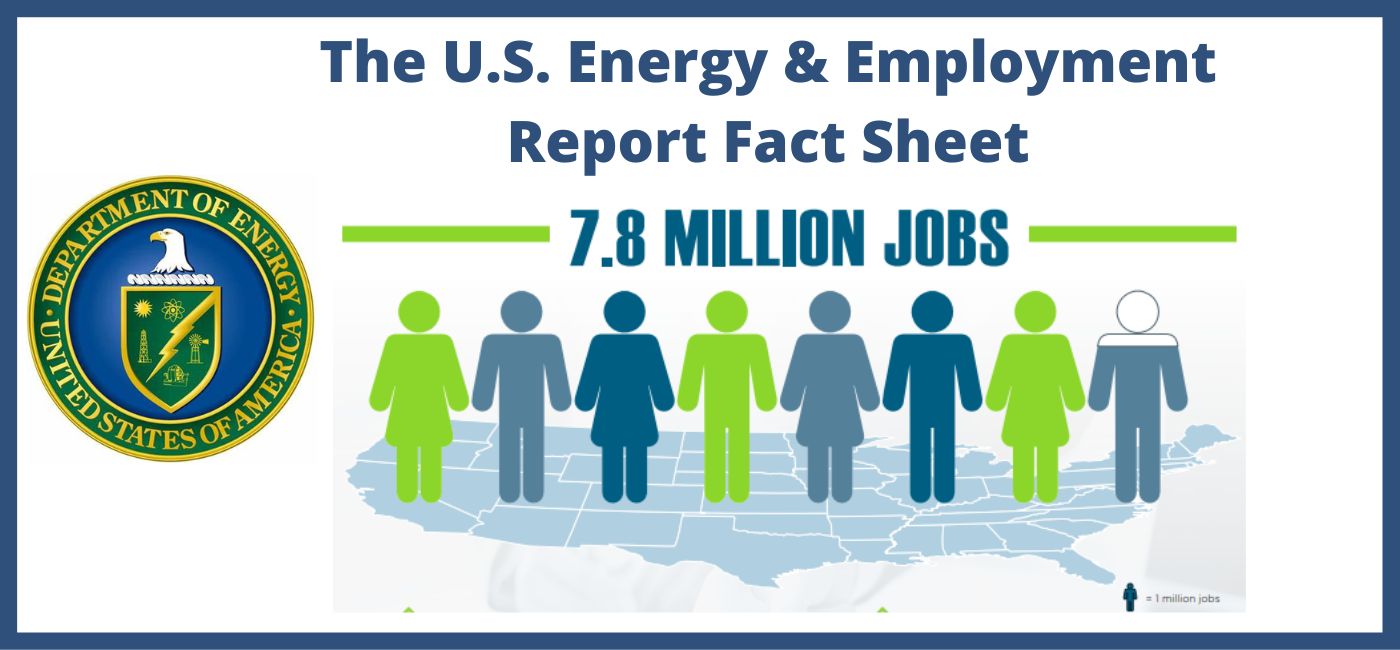
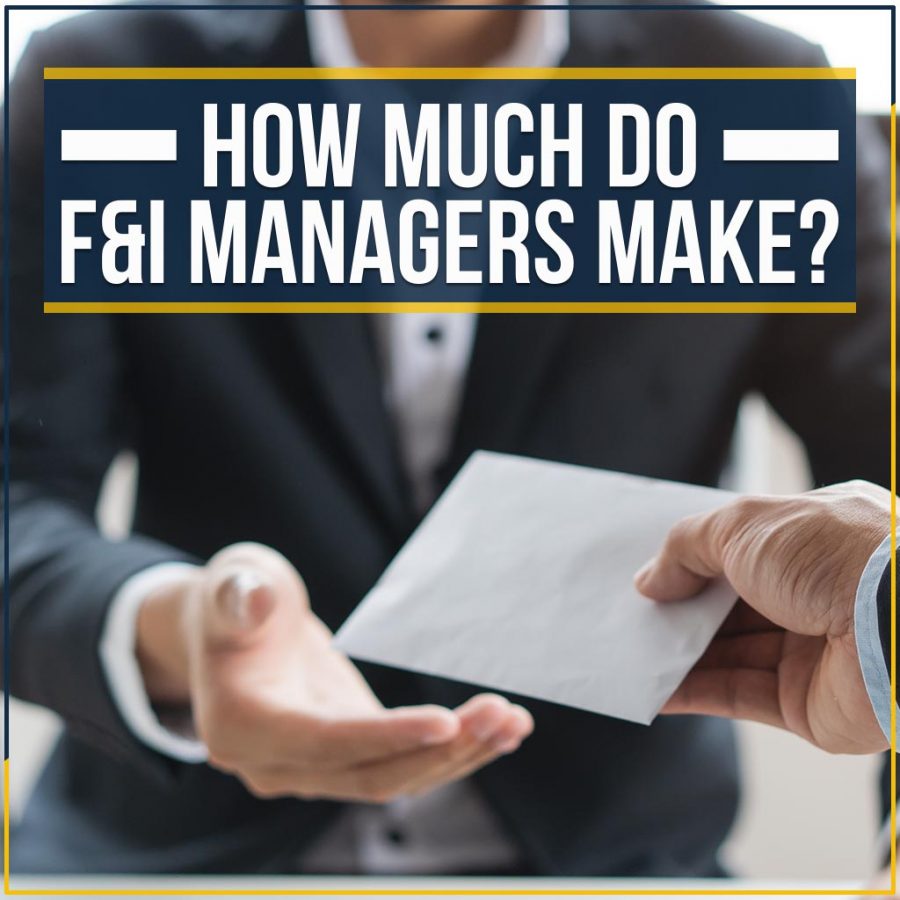
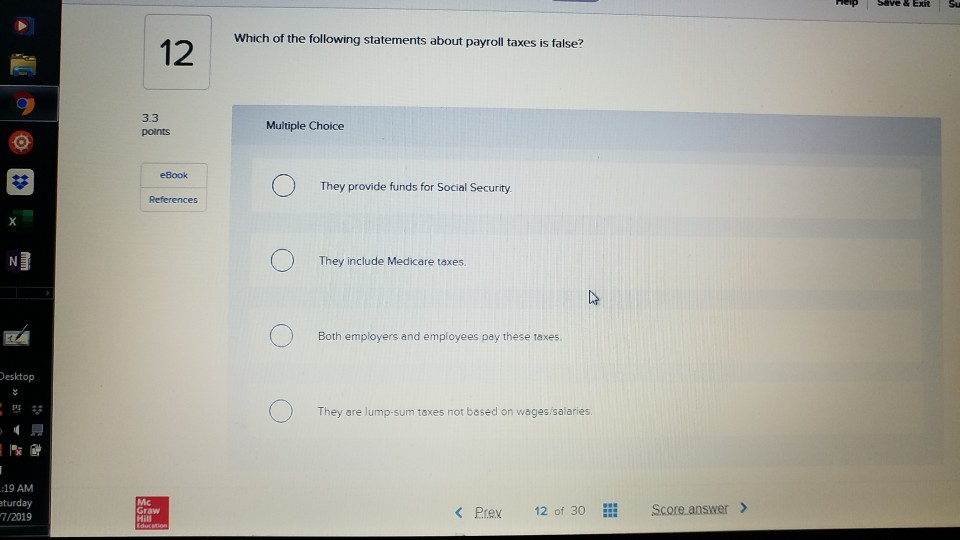
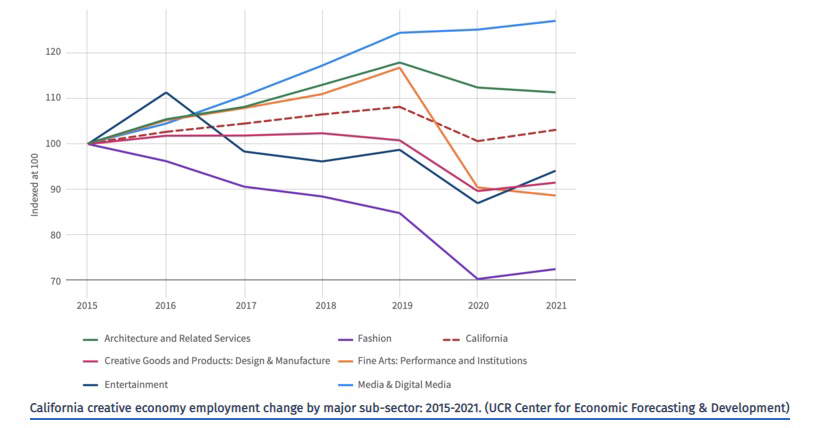
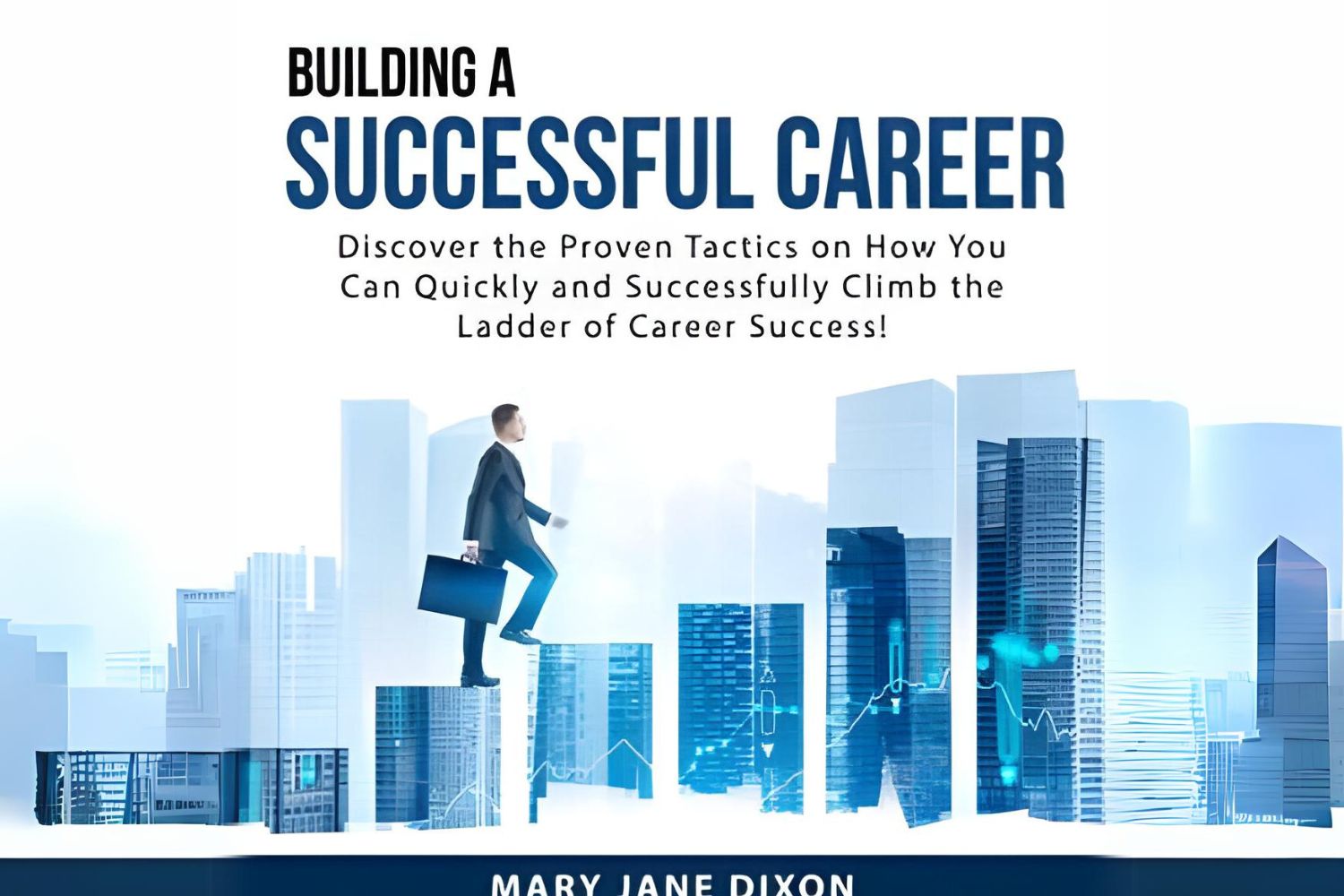
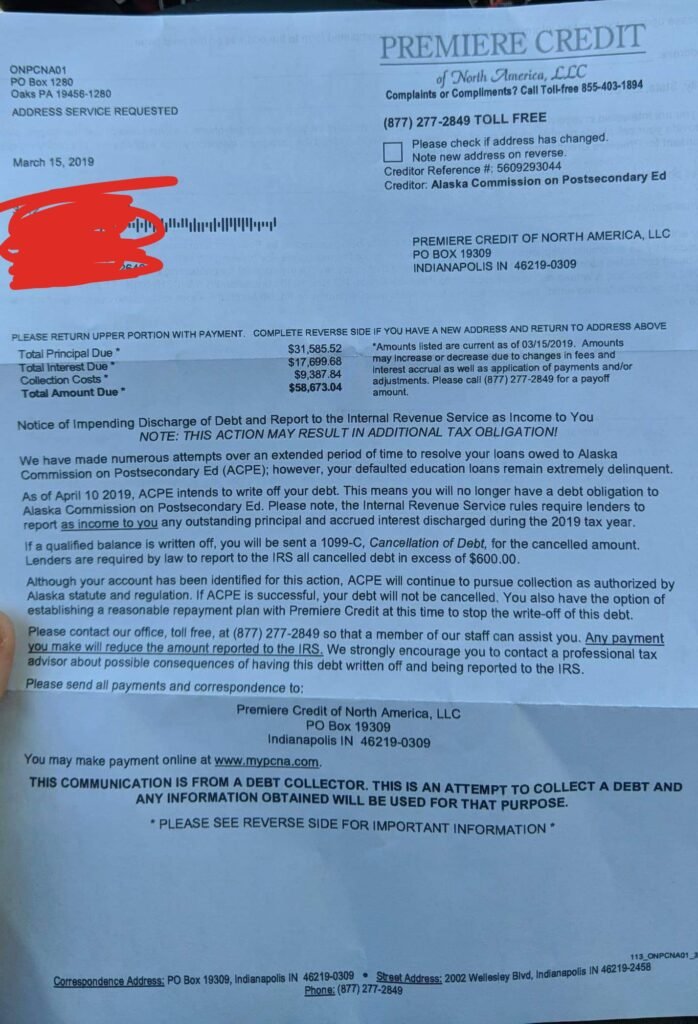
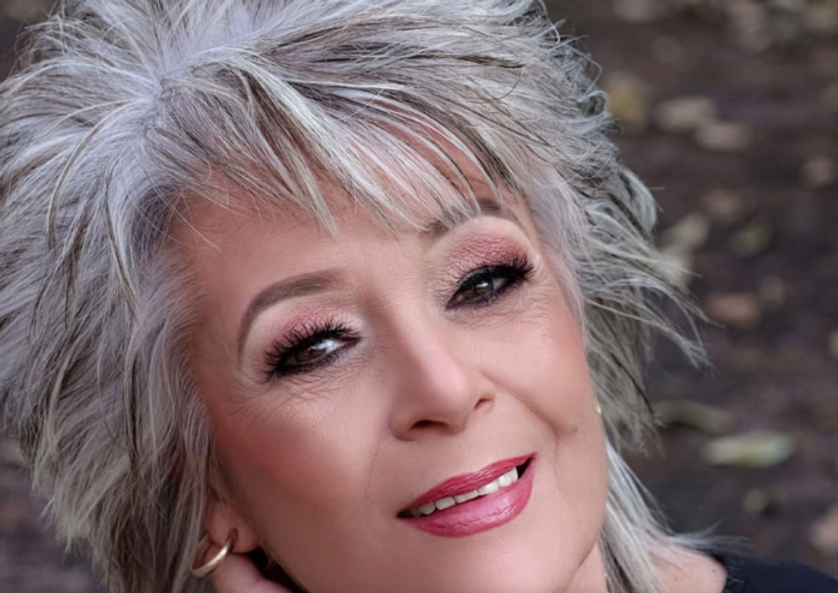
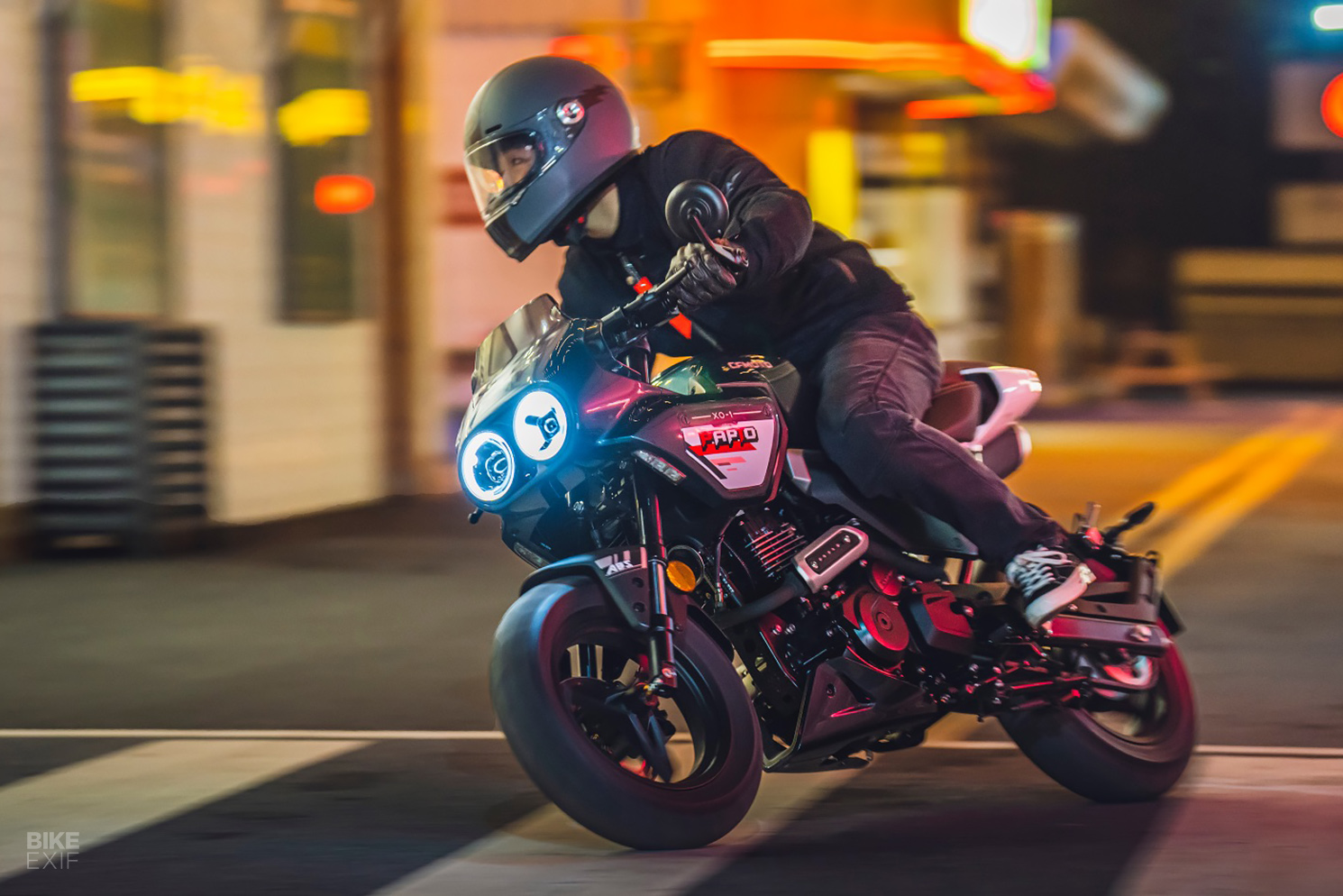
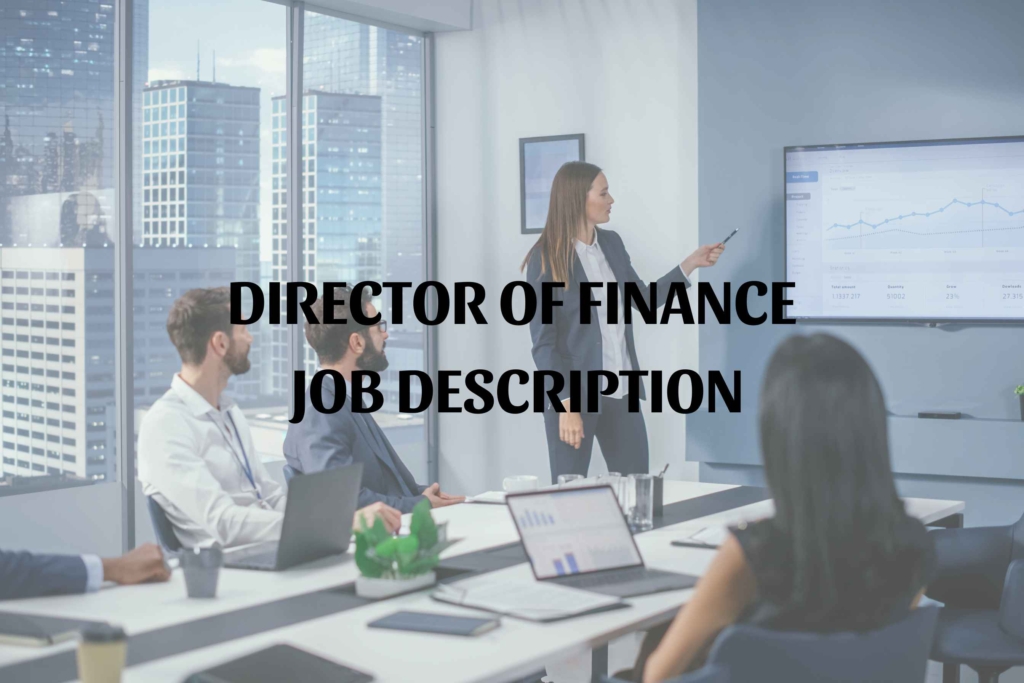
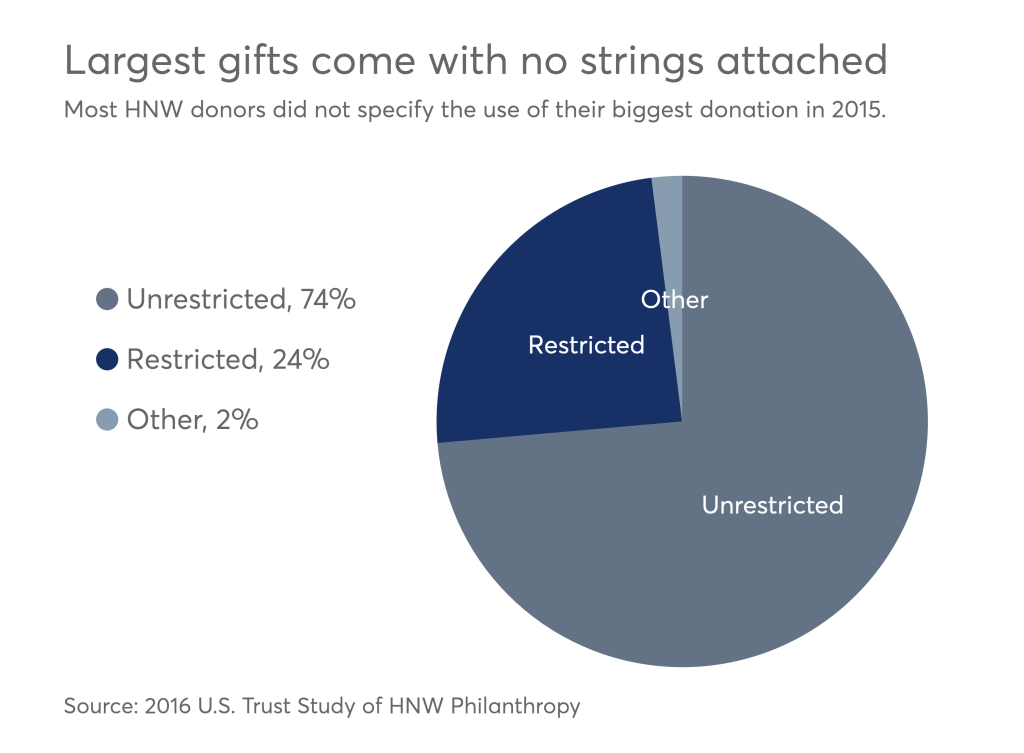
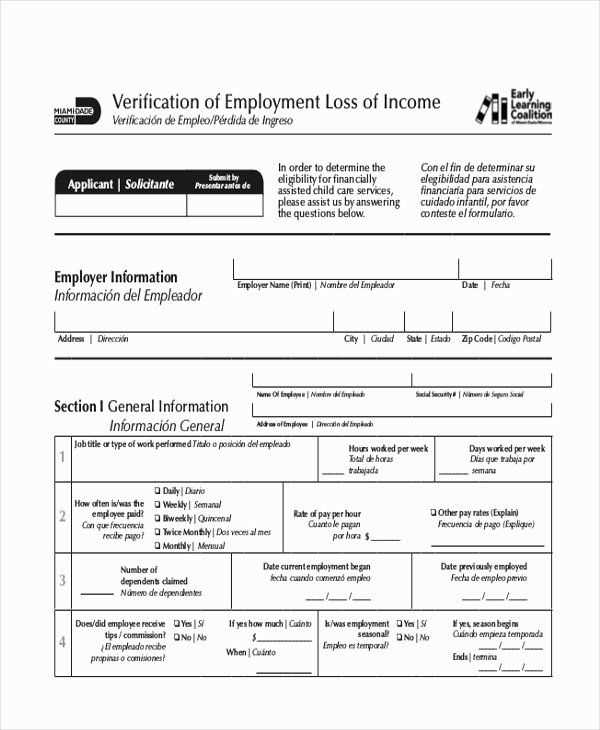
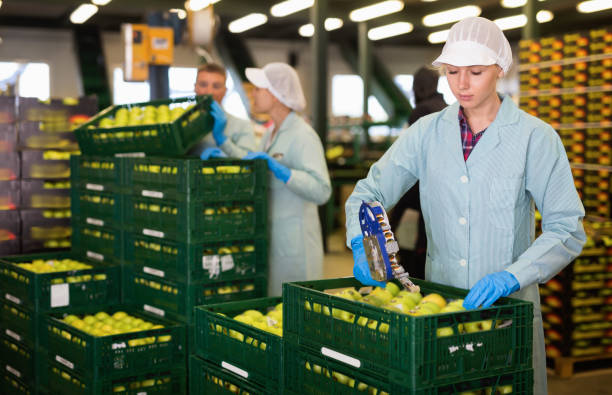